Types of hydraulic pumps
- rexroth distributors
- Jul 19, 2022
- 3 min read
There are generally three types of hydraulic pump structures found in mobile hydraulic applications. These include gears, pistons and blades. However, there are also clutch pumps, vacuum pumps, and dump truck pumps, such as Muncie Power Products' Dry Valve Pumps and Live PakTM.
A hydraulic pump is a component of a hydraulic system that takes mechanical energy and converts it into fluid energy in the form of an oil flow. This mechanical energy is taken from what is called the main engine (rotational force) such as the PTO or directly from the truck's engine.
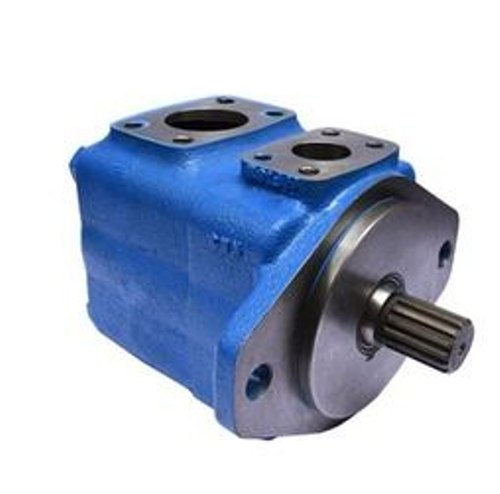

With each hydraulic pump, the pump will be of either a single-rotor or two-role design. As its name suggests, the single-rotating pump is designed to operate in one direction of shaft rotation. On the other hand, a bi-circulating pump has the ability to work in any direction.
Gear pumps
For truck-mounted hydraulic systems, the most common design in use is a gear pump. This design has fewer moving parts, is easier to maintain, is more tolerant of pollution than other designs, and is relatively inexpensive. Gear pumps are fixed displacement pumps, also called positive displacement pumps. This means that the same volume of flow is produced with each rotation of the pump shaft. Gear pumps are rated for maximum pump pressure rating, displacement in cubic inches, and maximum input speed.
Gear pumps are generally used in open center hydraulic systems. Gear pumps trap oil in the areas between the pump gear teeth and the pump body, move it around the circumference of the gear bore, and then force it out through the outlet port when the gears are engaged. Behind the copper alloy drive plates, or wear plates, a small amount of pressurized oil pushes the plates firmly against the gear tips to improve pump efficiency.
Piston pumps
When high operating pressures are required, piston pumps are often used. Piston pumps traditionally withstand higher pressures than gear pumps of similar displacement; however, there is a higher initial cost associated with piston pumps, as well as lower resistance to contamination and increased complexity.
The equipment designer and service technician must understand this complexity to ensure that the piston pump operates correctly with its additional moving parts, stricter filtration requirements, and stricter tolerances. Piston pumps are often used with truck-mounted cranes, but they are also found in other applications, such as snow and ice control, where it may be desirable to vary the flow of the system without changing the engine speed.
A cylinder block containing pistons that move in and out is located inside a piston pump. It is the movement of these pistons that pulls the oil from the supply port and then pushes it through the port. The angle of the discontinuous plate, against which the sliding end of the piston slides, determines the length of the stroke of the piston. While the powder plate remains stationary, the cylinder block, which includes the pistons, rotates with the pump's input shaft. The pump displacement is then determined by the total volume of the pump cylinders. Fixed and variable displacement designs are available.
Related Blogs
Rexroth hydraulic pump Rexroth hydraulic valve Eaton hydraulic pump Eaton hydraulic valve Rexroth a4vg A4VG Series Piston Pumps A10VG Series Piston Pumps PGH Series Internal Gear Pumps A4VSO Series Piston Pumps A7VO Series Piston Pumps A8VO Series Piston Pumps A2FO Rexroth hydraulic pumps Series PV7 Series Vane Pumps A10VO 52R Series Pumps A10VO 31R Series Pumps Atos PVL Vane Pumps Denison Vane Pumps External Gear Pumps Axial Piston Pumps Fixed Pumps Axial Piston Variable Pumps Open Circuit Dowty Gear Pumps Vane Pumps PV7 4WE6 Valves 3WH and 4wh Series 3WE6 Valves DB/DBW/DBDS Series ZD/ZDR Series Valves 2FRM Series Valves Directional Control Valve Z2S/Z2FS/SV/SL Series A6VM Series Piston Motors A2M Series Piston Motors 3A10VM Series Piston Motors
Comments